
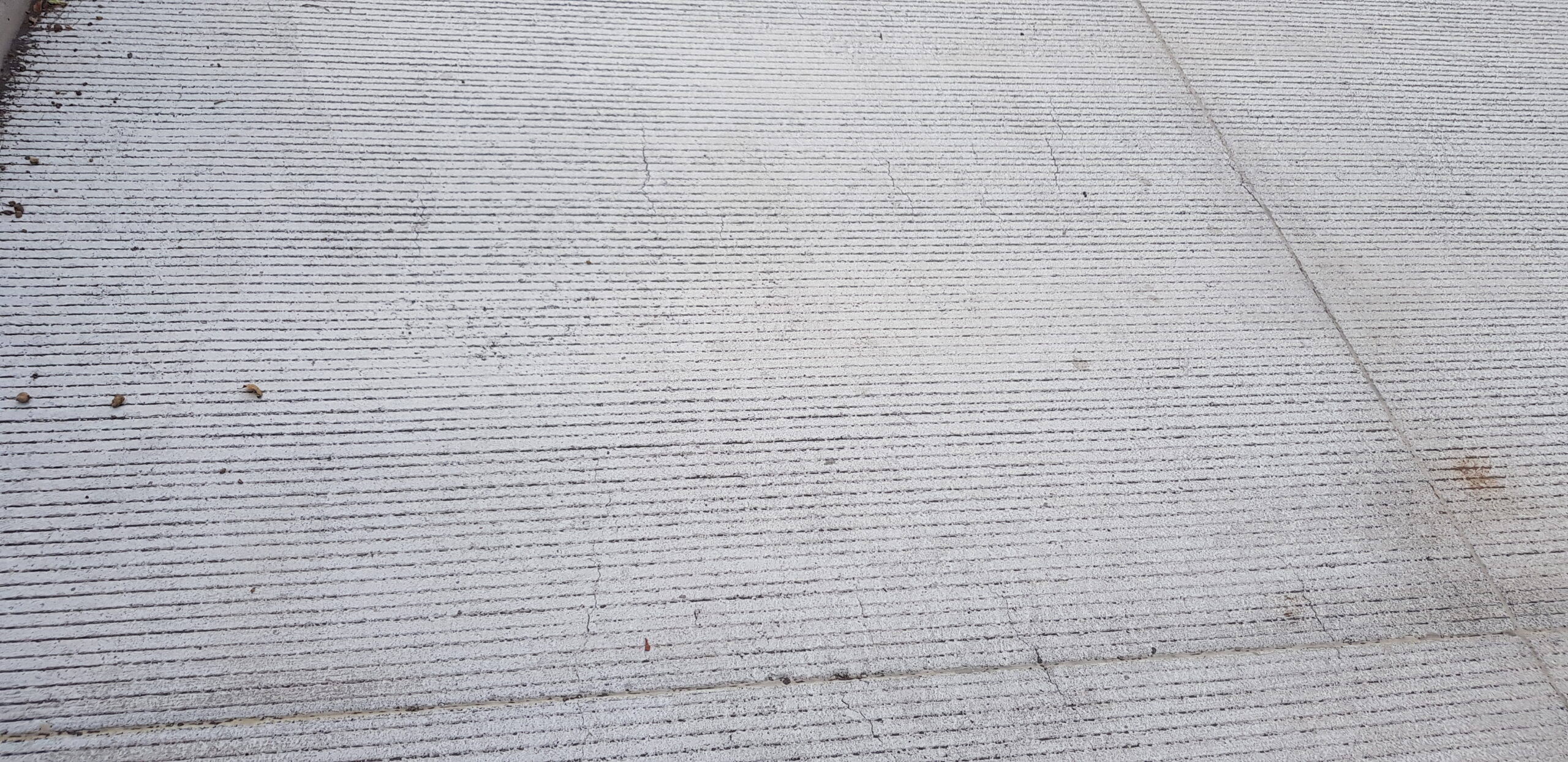
Agrietamiento por contracción plástica en pavimentos de concreto
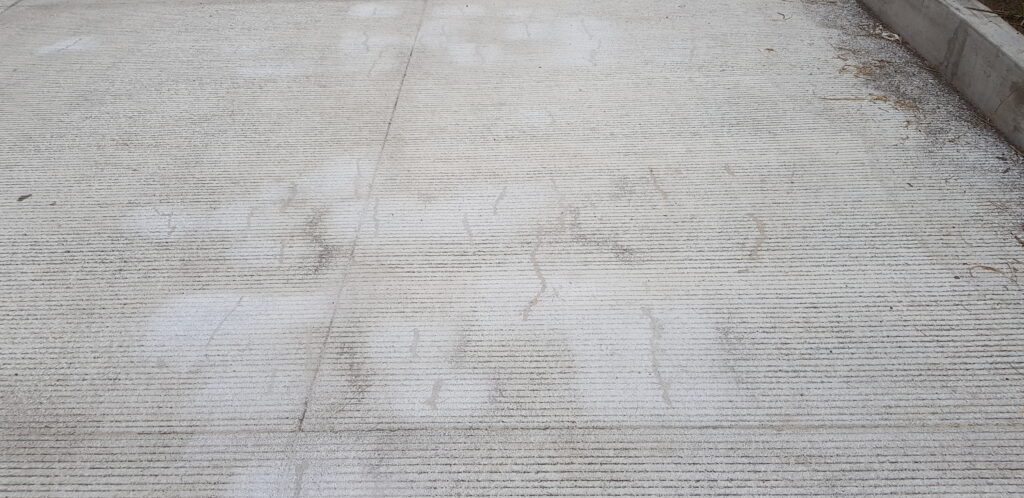
Este tipo de agrietamiento es el más común en los pavimentos y es causado por una rápida perdida de agua excesiva o una pérdida abrupta de este elemento en la superficie del concreto antes de que este haya fraguado. Este tipo de agrietamiento es un factor que alarma mucho por la estética de la superficie pero que no afecta la resistencia del concreto.
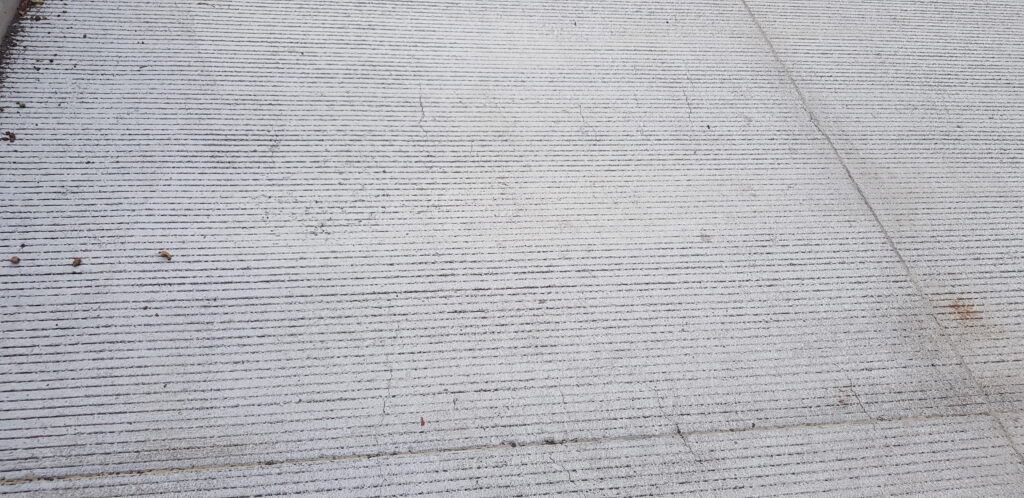
Para reducir el agrietamiento por contracción plástica es necesario identificar a tiempo las condiciones que lo provocan, antes de la colocación del concreto las medidas para contrarrestar el agrietamiento son las siguientes:
- Humedecer la base donde se colocará el concreto teniendo el cuidado de no saturar la superficie (empozamientos).
- Cuando existan condiciones climáticas adversas planificar la colocación del concreto en horarios donde se mejore el clima.
- En periodos muy calientes o con humedad relativa baja se pueden usar atomizadores de agua en la dirección del viento y sobre el concreto para que se forme una descarga muy fina de humedad que no altere la relación agua/cemento de la superficie.
- Comenzar el curado del concreto de inmediato utilizando membranas de curado.
- El uso de un aditivo retardante superficial es de gran beneficio en climas calientes y secos.
- Monitorear la tasa de evaporación para prever si se está perdiendo humedad superficial de forma muy abrupta. Esto se podría contrarrestar con barreras si estas fueran las causantes por excesivo viento.
LE GUSTÓ ESTE ARTÍCULO? COMPARTA AHORA:
Comparta en Telegram
Comparta en WhatsApp
Comparta en Facebook
Comparta en Twitter
Comparta en Linkdin
Comparta en Pinterest
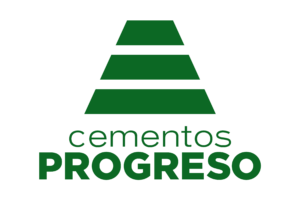
Investigación y Desarrollo
Cemento Progreso, S.A.